Water Testing in Los Angeles
As a testing only agency, we perform AAMA and ASTM standardized water testing throughout the greater Los Angeles and have been for years now. Our work carries us into multiple different areas of construction such as commercial, residential and industrial. Within these areas of construction we test everything from multi-story buildings to residential homes.
There’s a trend which we’ve noticed manifesting over the last number of years. The trend is minimization within the building design. Effectively, the stripping away of the bulkiness of the home in an attempt to make it more appear, well, more open, boxy, roomy or even streamline. It’s this manifestation that appears to be pushing this proverbial envelope of making buildings both esthetically beautiful while still maintaining functionality.
Here in California we don’t see rain making as much of an impact on design changes within residential construction. That is of course when compared to other conditions such as earthquake preparation standards and code.
Although there are standards which stipulate water runoff, slope, waterproofing and grade, it’s not typical that they evolve all that much. And there’s still the human component. Although there are these codes and standards in place, it still takes a human to enforce them, on site.
Residential and Commercial… not necessarily the same
The bulk of our work is in the commercial and public works sectors. However, we will still take on projects in the residential arena of construction as previously mentioned.
So we see both sides of construction. Commercial likes to be proactive with their water testing whereas residential is almost always reactive. Essentially water testing after an issue is discovered.
Moreover, it seems for whatever reason, residential new construction almost never incorporates quality assurance water testing into their specifications or drawings even though many residential designers incorporate commercial building products in their designs.
Contrast the residential sector to commercial design where water testing is written into just about every spec. Do they know something that the residential designers do not? Not necessarily.
So the question is…, is that bad that the residential designers omit any type of quality assurance testing? I’d have to say the answer is both yes and no.
Yes
If you have custom multi-million dollar buildings which by all accounts are really hotels and most with custom one-off finishes and/or custom installations. Buildings which incorporate millions of dollars in custom materials both inside and outside cannot afford repairs which may for by all accounts be classified as systemic.
Yes
If you’re a contractor who wants to get in front of any potential significant issue or design flaw. I believe like in commercial, some of these systems should be tested as a measure of quality assurance. An example of these systems might be decks, fenestration products and some grade to structure transitions.
No
If the building is your run-of-the-mill new construction tract house.
But the inspector passed it
With residential, one of the biggest complaints we hear from builders is that the city inspector signed off on the ______ (whatever was tested), so therefore the problem must be with our testing methods. Well, one must understand that the AHJ is still a human component and yet, still capable of making mistakes.
Our company tested 237 residential windows or window installations from 2017-18. Of those, more than half tested leaked or otherwise failed. With repairs approaching the millions on some projects, water testing in the early stages would have absolutely prevented most of these problems.
Yes this is new construction, And yes, they were all inspected as normal and every one of these buildings received a C of O.
The most common issue with this new trend of residential building
The most common issue we notice with this new trend of building is the transition from the interior grade to the exterior grade.The idea is to design this transition to be very close to flat. Within this condition we often times find a lack of slope but rather, level grade. This is in direct contrast to what’s considered historically typical such as a step up, sub-pan and/or even waterproofing between interior floor finishes to exterior grade elevations.
Keep in mind we’re not talking about hydrostatic pressures or moisture deriving from the slab. There are prescriptive measures in place to prevent that. We are speaking of water entering the building simply from the outside to the inside with normal rainfall, runoff or via irrigation.
Most people who have a pretty good understanding of the building codes understands that there must be impenetrable barriers around well, the entire building, the building’s envelope and grade. This is stipulated throughout the ICC Codes like the CRC or CBC.
Actual issues
Despite the fact that the grade was sloped 2% away from the home in “some places”, water still, enters the building as pictured here.
Designers are making every attempt to produce buildings with gracefully thin, streamline and / or seamless grade or sill transitions. This is evident even with the manufacturers such as the OTIIMA door system and others, catering to this new demand.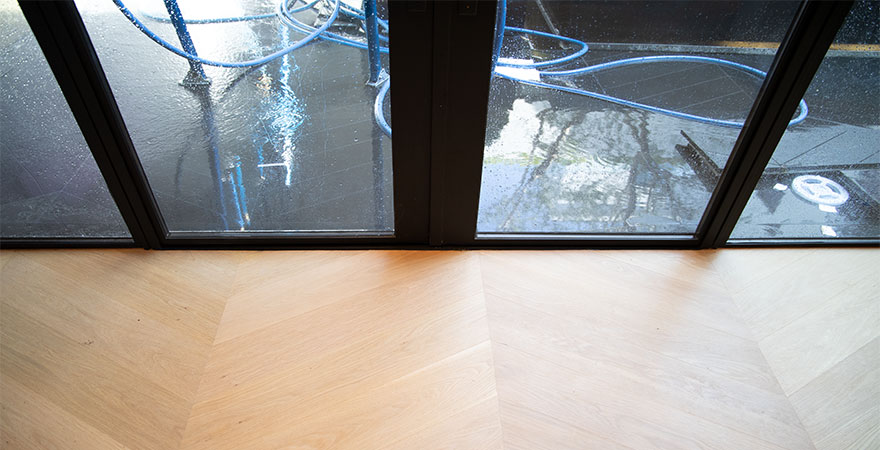
Exterior grade is equal to the interior grade here
Los Angeles Building Code Sets the Standards
CRC Section 4, R401.3 and R703.7.2.1 sets specific standards for how low the exterior grade is to be under the buildings weep screed and how the water is to be diverted away from the building. Effectively, Los Angeles residential building codes require grade elevation differences between the interior and exterior.
Most contractors who install fenestration products in buildings especially of a higher caliber and with these conditions, understand that panning in accordance with the ASTM 2112 is a good idea. On the other hand, one of the biggest challenges that contractors will face with these grade to grade installations is that it’s just flat-out difficult to install door and window pans effectively, and have them perform as expected.
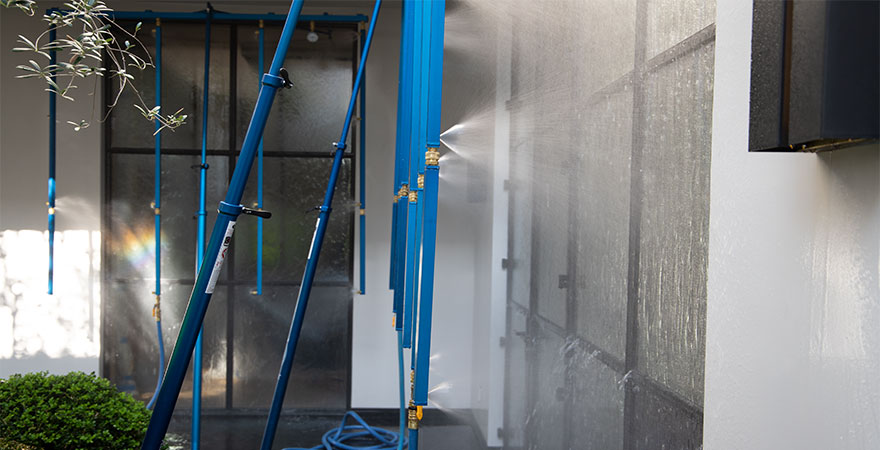
Performing water testing of windows
It’s important to realize that because this type of modern grade to grade construction is becoming increasingly common throughout the Los Angeles area, many times, the water intrusion goes unnoticed.
With time, what ends up happening is water will travel under the flooring and can, for many feet with no indication. Therefore, for testing purposes, the use of an infrared camera is absolutely required when doing this type of water testing.
After a while and depending on the flooring type, stains and / or material warpage may eventually develop. Ultimately necessitating testing of the fenestration products or wall systems. And, the remediation of the condition which may include mold and interior finishes.
The example below are infrared images taken from a couple houses in the Los Angeles area. Both have the same grade transition design and subsequently identical issues. Both were from the different builders. Both with interior wood floors for their flooring. And, although the floors were a different species of wood, both nevertheless leaked the same.
These grade to grade installations
In our two examples, the window and door systems sit flat on grade. However, once we performed destructive testing, we noticed that the doors and windows appear to have been raised by a mortar bed which was installed inside the pan, thus increasing the height necessary to accommodate the interior finishes. This raising of the doors and windows was achieved by filling the sill pan(s) solid with mortar.
Those reading should also know that we only performed destructive testing on one system type as pictured below.
The fix for this condition doesn’t come easy and isn’t cheap. In the majority of these types of cases which we test, the contractors will move to the exterior for solutions. In most cases it’s because of the permanent nature of the fenestration product coupled with replicating the buildings exterior and interior finishes which are again in many cases, custom.
I see that without additional methods to eliminate water intrusion, and relying on people to apply these almost stop-gap-like methods of various sealants at the grade connections as the only means of water penetration resistance. Effectively you’d be relying on two things to keep water out of the building.
- Just a sealant which may or may not break-down over time.
- The application / applicator. The sealant is only as good as its installation. For the application there can be air pockets or poor adhesion which will result in interior leaks. As for the actual person applying the material… who knows, he/she may have had a bad day or is hungover while applying your only measure of water resistance. I’m just sayin…with what we’ve seen, you never know.
Standardized testing through AAMA and ASTM
Water testing in Los Angeles fenestration and walls are standard procedures in commercial or public works. It’s referred to as quality assurance testing. AAMA and ASTM produced these standards which we and others must adhere to while conducting these tests. Contrast this to the private residential sector where testing is almost never required. And if water testing was performed, most times it’s performed by the installers.
This type of testing is normally performed with no AAMA or ASTM standard in mind, completely unregulated. Like with a water hose on full blast for example. A great many people have no idea that testing like this without the proper standard or equipment could be considered “over-testing”. Essentially over testing is when a product gets tested with too much pressure or water thereby forcing a leak that may not have ever occurred otherwise. This is also known as a false positive.
On the other hand, with residential… testing is usually only called upon to resolve a known issue such is the case with forensic testing. The standards which we test to can be found in these documents ASTM 511-08 or the ASTM 2128. These ASTM standards effectively encompass the testing of decks, roofing systems, walls and fenestration products alike.
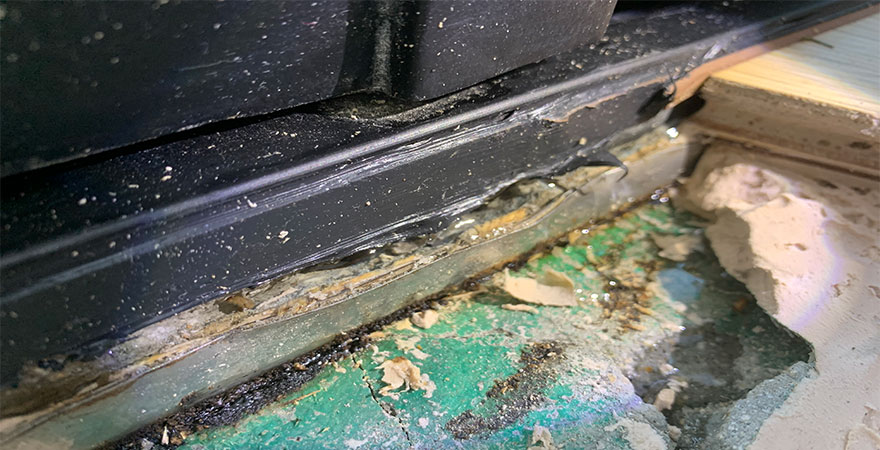
Sill sitting on the top of this door pan with water overflowing the pan (by-passing pan)
Other uses of water intrusion testing
With real estate transactions, testing is often times necessary or is an effective means to determine whether a water stain is active or otherwise repaired. Of course, this doesn’t apply only to walls or fenestration products. Ceilings are a common place where stains are often times questionable. We find that the majority of interior residential leaking are plumbing related. With the exception of course with leaking from flat roofed or A-framed ceilings and under decks for example.
Testing is a costly and time consuming process. For many realtors there just isn’t enough time in an escrow to perform qualitative testing. In contrast, our water intrusion testing in the insurance and legal industries is often necessary for discovery.
For others, specifically residential, it’s a good idea to have at least a sample of newly installed fenestration products or custom systems tested in the beginning of the project before interior or exterior finishes have been applied. At least that way, the contractor will have an opportunity to modify or otherwise improve the installation procedure if it’s found to be flawed. Thus, saving hundreds of thousands or even millions in future damages.
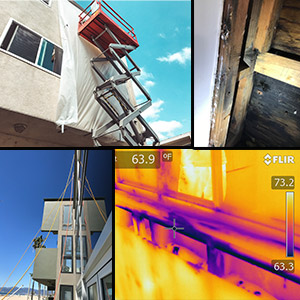
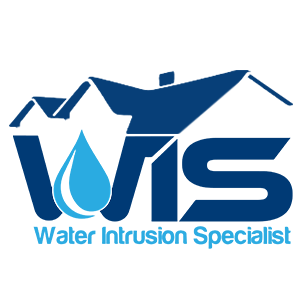