ASTM D5957 Test Method:
Standard Guide for Flood Testing Horizontal Waterproofing Installations (Field Quality Control Test)
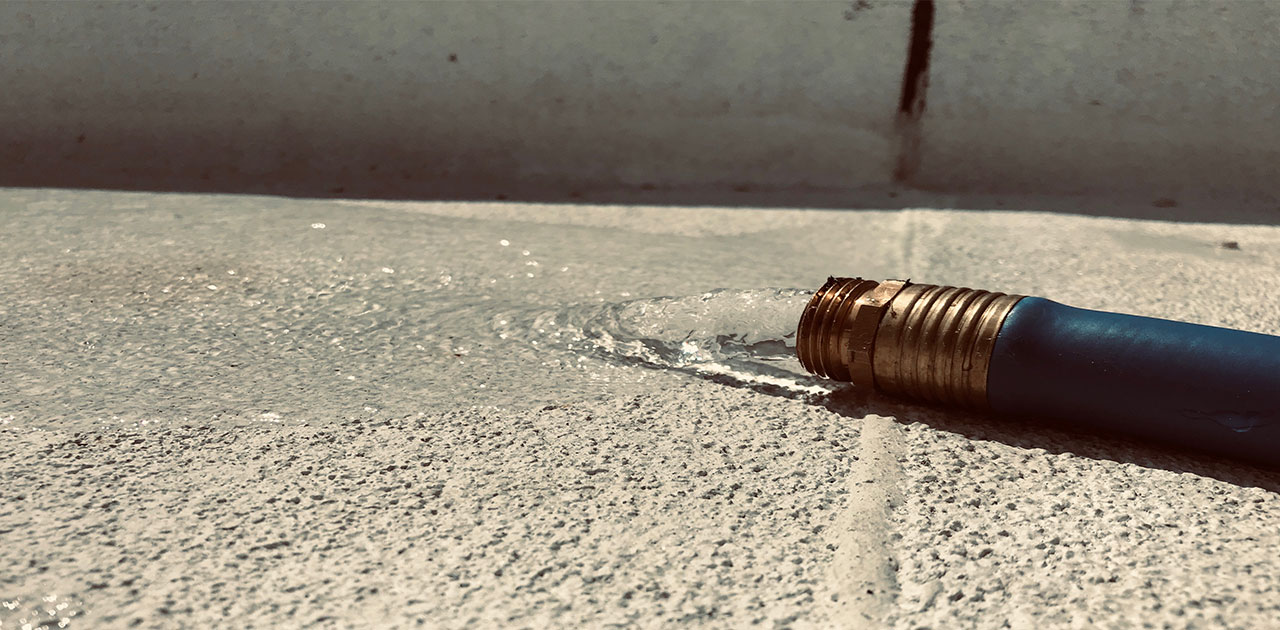
What is the Scope of this Method?
The ASTM D5957 provides guided methodology for testing the water-resistance ability of waterproofing installations that have been installed to horizontal surfaces and the slope must be no greater than 20 mm/m (2% slope) (1/4” per ft).
Which Products & Systems is this Test Applicable for?
This test would be applicable for liquid (fluid) applied membranes, fully bonded (adhered) sheet membranes, and/or any loose laid sheet membranes of waterproofing installed on/at:
- Waterproofed Garage Parking Areas
- Waterproofed Decking Systems
- Special Note: This test ‘is not’ intended for use on home or building roofing systems.
The Test Protocol Explained:
This test is not typically performed until all waterproofing membranes and flashings have been thoroughly inspected by Design Professionals (i.e.-Licensed Architects and/or Engineers). Any deficiencies found by such qualified inspectors must be repaired prior to testing. Testing usually takes place when just the waterproofing membranes are exposed (prior to the installation of any additional layers being added).
Before any water can be dispersed a full containment assembly must be constructed and it must be nondestructive and easy to remove after testing. It cannot, for whatever reason, penetrate the waterproofing it must test.
- Containment
- Typically made of plastic sheeting that is adhered to the surface of the waterproofing membrane by means of a seal (i.e.-tape). There is usually and overflow system built in, if needed, at 5 inches above the low point on the test surface so as not to exceed the structural capacity of the substrate (a licensed structural engineer must review the entire process before testing can begin)
- Water Loss Monitoring
- Any loss is monitored by means of tape marking (in 1/8-inch increments) or by using alternative instrumentation measurement techniques that incorporate the use of scale, and in at least two (2) locations.
- Flooding the Test Area
- After all of the proper precautions and inspections have been made the area is flooded with water to receive a minimum cover of 1-inch, but not to exceed a maximum water depth of 4- inches at it’s lowest point. The water height is then held so as not to exceed a minimum level of 2- inches below the edge of any flashings.
- Duration of Test and Observation
- The test is performed for a minimum of 24-hours and a maximum of 72-hours. There must be no rainfall forecasted to occur. If any water leakage is found during the test duration the water is to be immediately drained from the test area (zone). T
What is the Final Result?
This test method and process is considered to be final if no water leakage is detected during the aforementioned test period. If the products/systems do show water leakage, additional forensic investigation (that is outside the scope of this test method) may be required. Typically, after any noted leakage the contractors and design professionals investigate, remediate, and retest.
5-Essential Areas of the Deck which are Vulnerable to Water Intrusion
- Railing connection into the deck membrane
- Deck to wall flashing
- Topcoat or waterproof membrane
- Drains located in the deck
- Parapet walls surrounding the deck
Note-1: WIS no longer performs this test due to simplicity of general contractor to perform in conjunction with the Design Professionals and Inspectors of Record (IOR).
Note-2: For forensic leak investigations feel free to call us at 888-381-7377 or Contact Us Here.
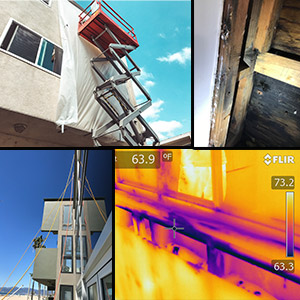
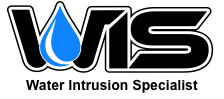